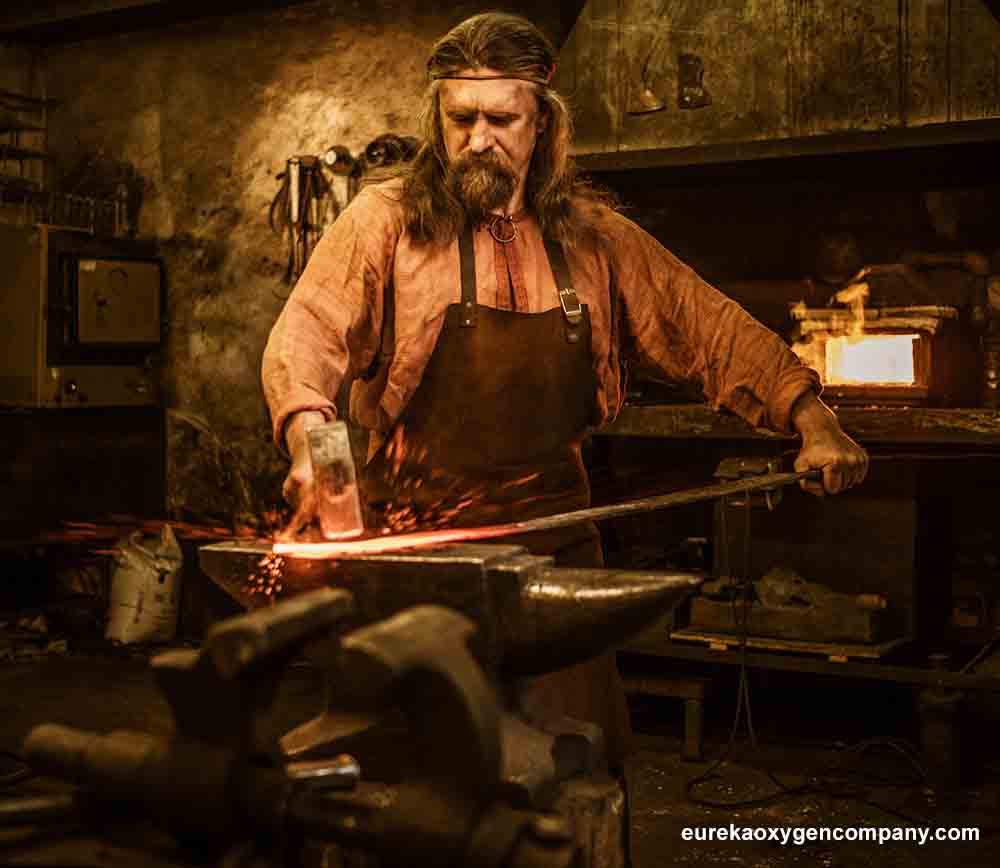
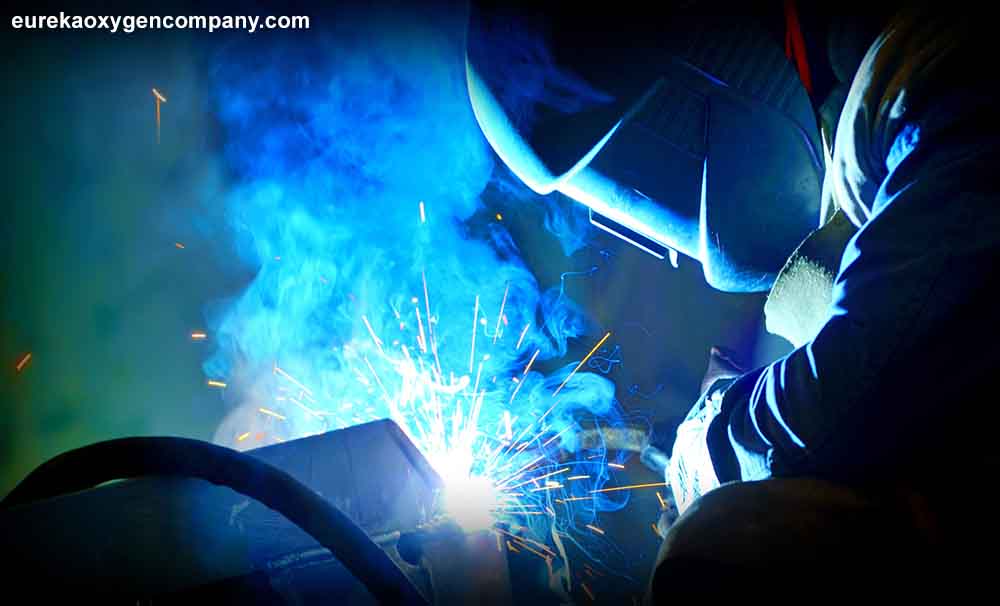
Welding as we know it today didn’t come into existence until the late 19th century. Two members of the Davys family each developed their own discrete form of welding, and those two branches became the foundation of the two available approaches to welding for almost a century – acetylene and arc (stick). There were multiple modes for containing and stabilizing the acetylene during this developmental period, and the initial arc method invented by Humphry Davys involved two carbon sticks and the arc passing between them. This method is still used today to weld galvanized sheet metal with copper-bronze filler material, due to the low heat generation involved.
The formation of the American Welding Society in 1919 signaled that welding had arrived as an industrial process worthy of control and standardization. Subsequent developments include the introduction of Shielded Metal Arc Welding (SMAW) which also remains in use today. Then came the use of inert gases rather than solid coatings as the shielding medium, beginning with helium and then argon. Both are still in use today, in varying proportions for different applications. This was Metal Inert Gas (MIG) welding, until CO2 (not inert) largely supplanted the inert gases, causing the American Welding Society to rename the process as Gas Metal Arc Welding (GMAW). Two subcategories are spray transfer, which allows greater deposition rates thanks to the addition of oxygen to the gas blends, and short circuit, which allows welding of thinner metals.
