A superior welding process is well noted for delivering two key benefits, which are weld integrity and weld repeatability. By mastering the ideal techniques, you will always be able to produce strong and long-lasting welds that are devoid of cracking, spatter, porosity, distortion, undercut, and even erratic beads. Generally speaking, superior quality welding is essentially a mixture of cleanliness, proper materials, and consumable storage, welding types, and the type of gas you utilize. Here then are a few tips on how to greatly improve your welding quality as a beginner.
Always place a strong emphasis on cleanliness
Cleanliness is always an integral part of producing quality welds. Should you fail to take the necessary time to clean components you wish to weld, the outcomes will often be disastrous. When contaminants like dirt, grease, dust, or even paint infiltrate your weld, they will give rise to issues such as porosity, unsightly beads, incomplete fusions, cracking, and so on. In their turn, all these welding problems can affect weld performance, durability, and how it can withstand corrosion.
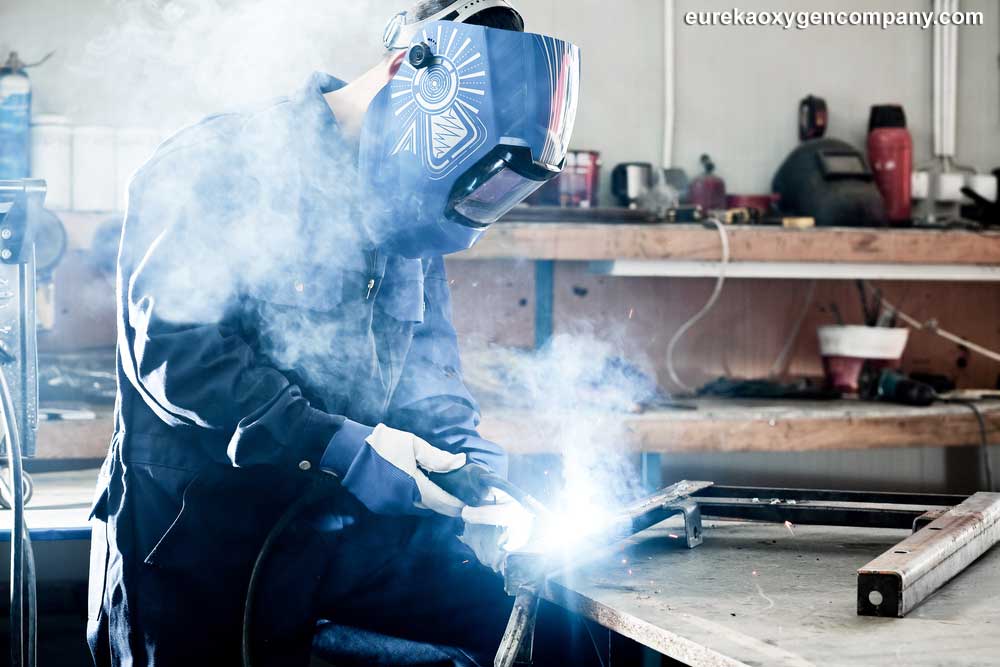
To this end, your process ought to always incorporate a thorough cleaning routine of all components you wish to weld. This goes a long way in ensuring surfaces are spotless and smooth. It also guarantees consumables, welding equipment, and your working environment are always clean and free of contaminants. As such, always make sure dirt, dust, grime and grease are eliminated in order to leave the components you want to weld are clean as possible.
Store consumable welding supplies in the right way
This is often a very downplayed part when it comes to how to improve welding quality. It is very important to store consumable welding supplies in the proper manner to guarantee they are, at all times, contaminant-free. When you do this, you will be in a good position to circumvent quality challenges including excessive slag fluidity, rough weld surfaces, porosity, and even problematic slag removal. Always ensure filler wires, grinding wheels, and the glove you utilize to handle materials are stored in a clean, dry place. Also, make sure you strictly abide by the storage instructions outlined by their manufacturers, especially for electrodes and wires. Some electrodes used in welding need to be stored at specific temperatures. While some wired need to be stored at given humidity levels.
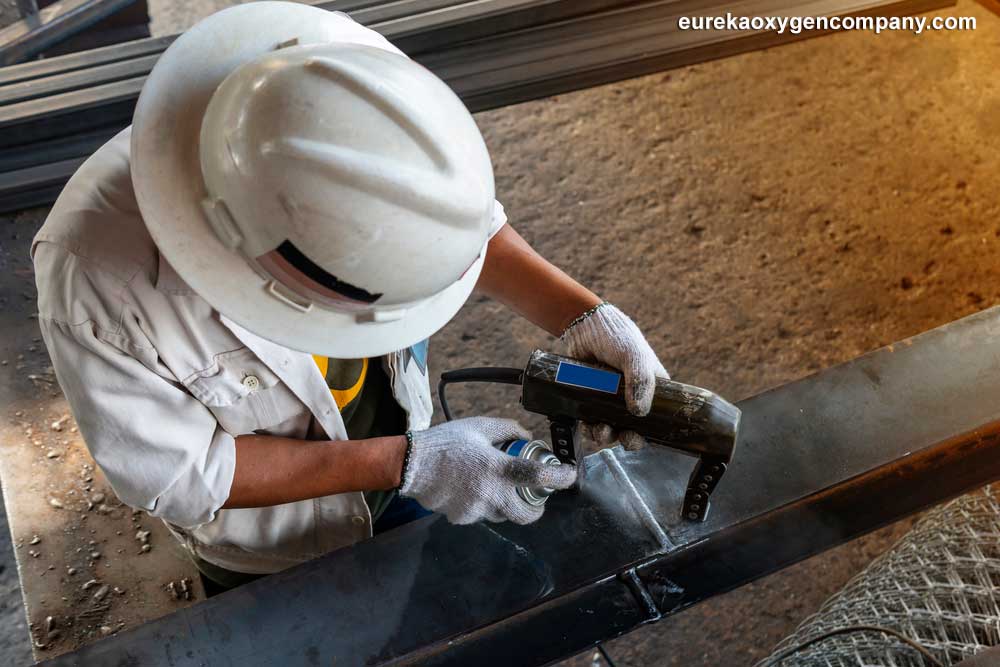
Always check your tips before performing welding
The tip of your welding gun is what ensures your wire remains straight as it issues out of the gun. There are usually two problems with a tip that can impair your weld quality. In the first place, tips can accumulate dirt at their bottom sides. This occurs when dirt ends up on the wire and makes its way to the tip where it builds up. When this happens, the welding wire will be stuck and get jolted, and this triggers irregular weld patterns. So, always keep a close eye on your tips and clean them on a regular basis.
On the other hand, over time, your tips could get worn out. This will make the wire fail to move in a straight pattern. When you notice such patterns, make sure you replace the tip.
Choose between push and pull welding methods
One of the most frequently used welding methods is “pushing” the gun towards the direction of the weld otherwise known as the forehand method. Yet another popular technique is “pulling” a weld also referred to as the backhand technique. The first technique is suitable for producing flat and aesthetically pleasing welds since it doesn’t penetrate deeply. This method is recommended whenever the appearance of your welds must look attractive. On the flip side, the pull welding method produces deep welds that penetrate and tie into the base metals with strongholds. This technique is well suited for making welds that need to hold to something.
Set the right amperage for different welds
Failing to set the suitable amperage for your welder can give rise to problems depending on the exact kinds of metals you wish to weld, the penetration you desire to achieve, and even wire speeds. The main factor in terms of why you should set an ideal amperage setting is it will always determine how deep you may penetrate your weld. When welding thin metals, the right amperage setting is lower, while for thick metals, higher settings are recommended.
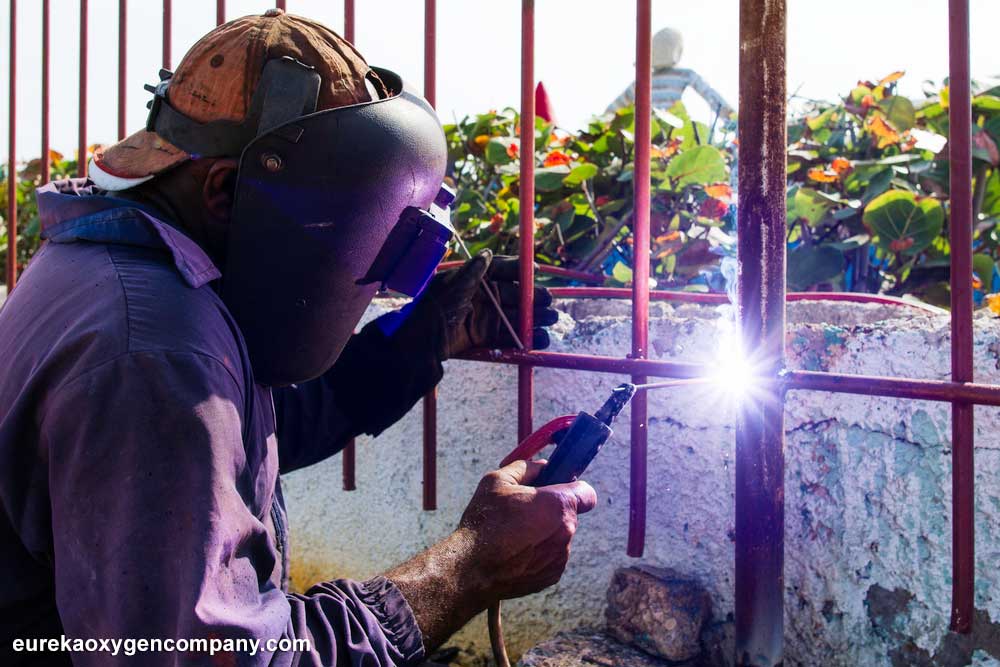
Understand your welding conditions
When you weld indoors in controlled environments, the welding process almost always moves very smoothly. On the other hand, working outdoors may significantly influence the quality of your welds, depending on the exact conditions you work in. For example, too much wind can make your shielding gas to blow away, and this will prevent the weld from penetrating deep. Alternatively, welding in rainy conditions or in close proximity to a puddle of water can cause serious safety risks including receiving an electric shock.
Another welding safety best practice is never weld in the outdoors during a lightning storm as it could endanger your life. Lastly, welding in snowing weather or very cold conditions is frowned upon since it prevents the weld from penetrating deeply because the base metal will be extremely cold.