Shielding gases have been in widespread utilization ever since the early 20th century, and have now evolved to be an essential part of commercial and industrial welding processes. With the passage of time, it became evident that blending gases with varying characteristics is often advantageous in a number of different applications. One of the most commonly utilized industrial gas mixtures is the argon and oxygen blend. Mixes of argon and oxygen are well noted for delivering numerous benefits, particularly when contrasted with other alternative shielding gases or even their mixtures. Let us now take a closer look at why argon-oxygen blends are in high demand in the welding sector.
Why mix argon and oxygen in welding?
Argon is classified as a noble gas or otherwise known as an inert gas. For those who might perhaps be in the dark, a noble or inert gas is one that cannot react with other elements in its proximity. This makes argon very ideal when a welder works with particularly reactive metals. To this end, argon is often made use of as what is termed a shielding gas. The key function of shielding gases is protecting the weld pool against external influences or even contaminants.
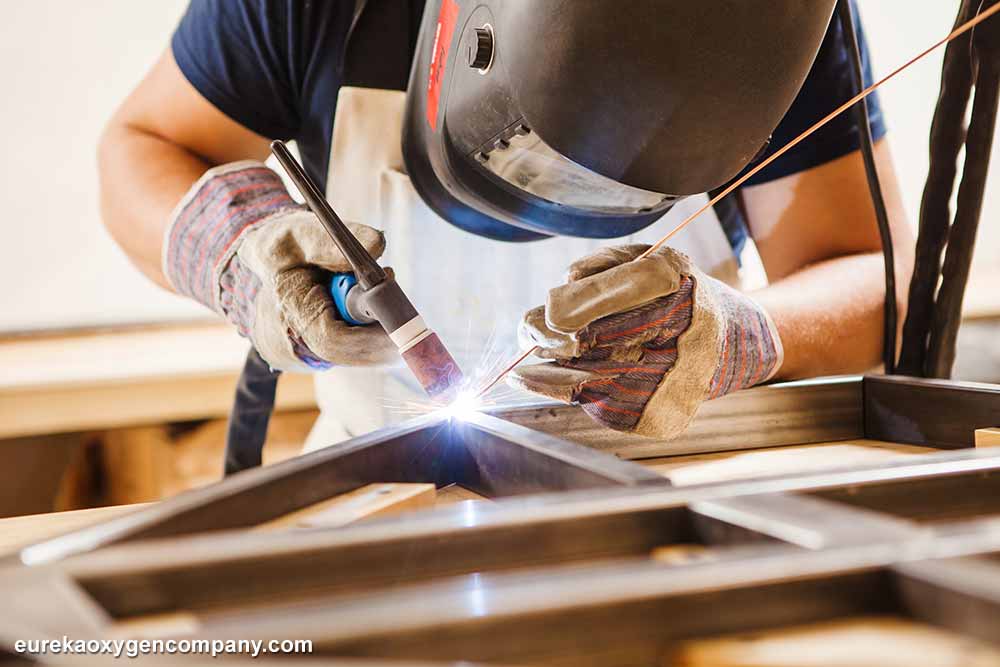
This, of course, includes offering sufficient protection from atmospheric factors including oxidation and nitrogen absorption. Shielding gases such as argon are also useful in stabilizing the electric arc.
However, using pure argon in welding always comes with a number of shortcomings that can impair its capability to guarantee the integrity of welds and arc stability. So, the only solution to circumvent these issues is introducing another suitable gas to make a blend that suits the exact application you may have in mind.
The addition of diminutive levels of oxygen to argon has been proven to immensely improve the shielding gas’s fluidity and even the overall quality of the weld deposit. Oxygen, when blended with argon, can effortlessly serve as an active shielding gas as long as its concentration is below 10%. It as well goes a long way in contributing the prerequisite high energy and heat levels to welds. Oxygen facilitates nearly all burning processes by simply augmenting temperature levels and combustion rates. Therefore, in this case, adding decreased levels of oxygen to argon improves on the shortcomings of using pure argon. By improving heat transfer, oxygen can fast-track droplet rate and even keep the weld pool in molten condition for prolonged periods of time. In turn, this allows the metals you might be working on to flow and eventually fuse much more consistently across the weld and flatten the bead.
What are the main welding applications of argon-oxygen mixtures?
Typically, argon-oxygen blends are utilized in the welding of heavy-section carbon steels in the manufacture of a wide variety of products. This includes farm equipment, automotive assembly, ships, military transports to mention just a few. Also, these industrial gas mixes are used in spray arc welding of ferritic and austenitic stainless steel components. Argon-oxygen mixtures may also be made use in gas metal arc welding of stainless steels and carbon steels metals.
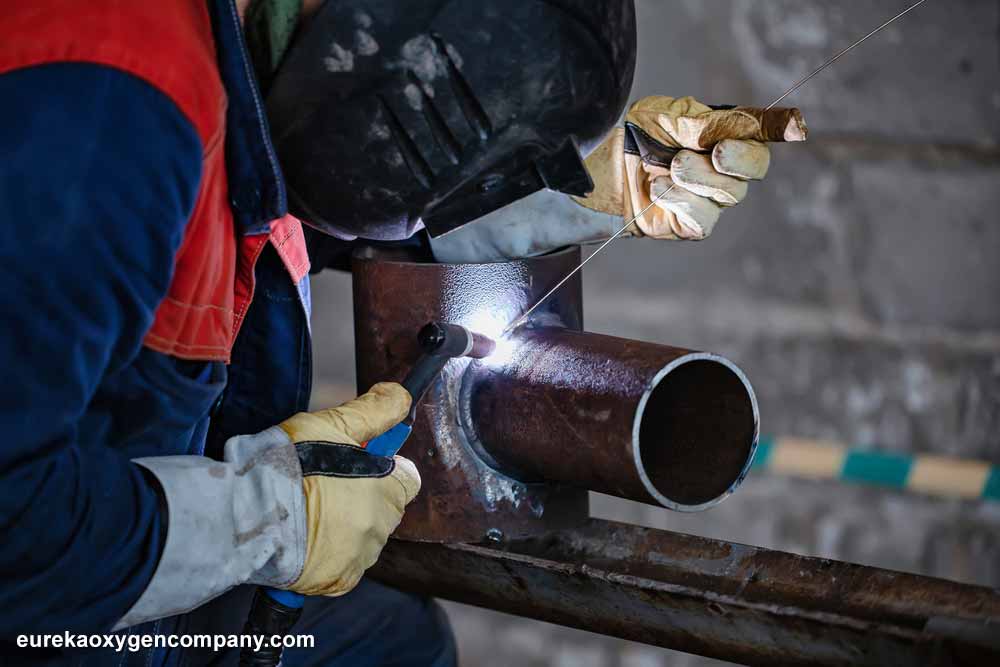
Let us now briefly review the various blends of these industrial gases which are commonly utilized in the welding sector.
Argon-Oxygen (99% -1%)
This given blend of argon and oxygen is mostly utilized in the spray transfer of stainless steel. In this particular application, the ratio of the mixture is more than sufficient to effectively stabilize the arc. While at the same time, improving the droplet rate and bead appearance.
Argon-Oxygen (98% – 2%)
This mix is a suitable solution for spray transferring stainless steels. It is the blend of choice for spray arc welding carbon along with a number of low-alloy steels. In this application, it is acclaimed for producing more wetter action when compared to the 1% oxygen mix. Still, it is known to produce a darker bead appearance.
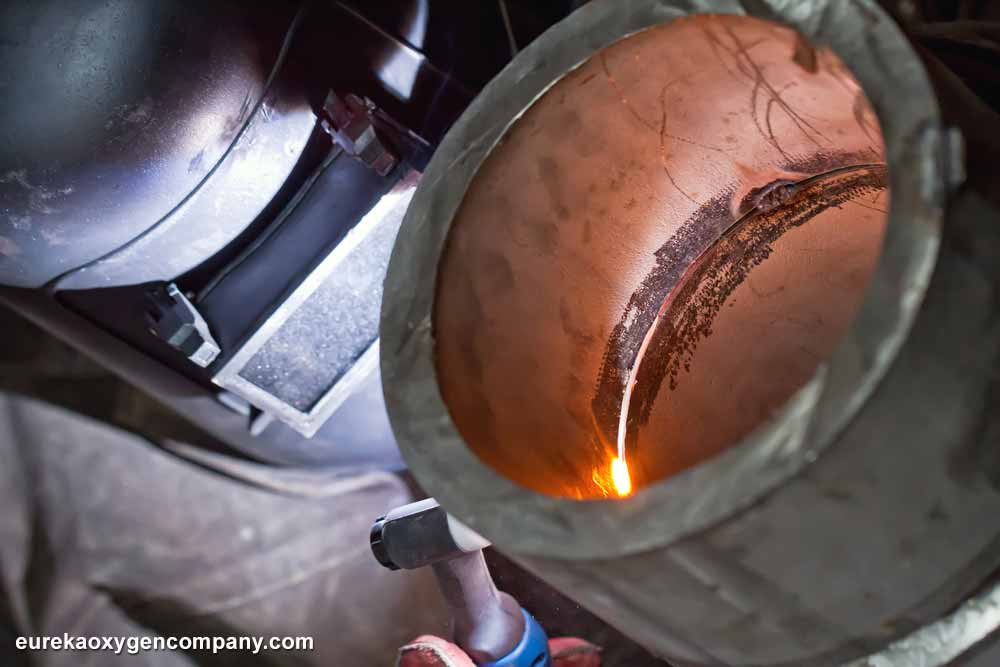
Argon-Oxygen (95% – 5%)
The 95% Argon 5% oxygen blend is the most preferred solution when it comes to welding general carbon steels. It is noted for delivering a markedly more fluid, but controllable weld pool and much higher travel speeds when compared to the other mixtures.
What are the main benefits of argon-oxygen mixtures in welding?
As it was previously stated, blended mixes of argon and oxygen can deliver many benefits when contrasted with other alternative shielding gases. Some of the most notable of which are guaranteeing substantial operational cost reductions and improving overall weld quality. Using these industrial gas mixtures lets welders produce high-quality welds, especially when they make use of either short arc, spray, or pulse spray modes of metal transfer.
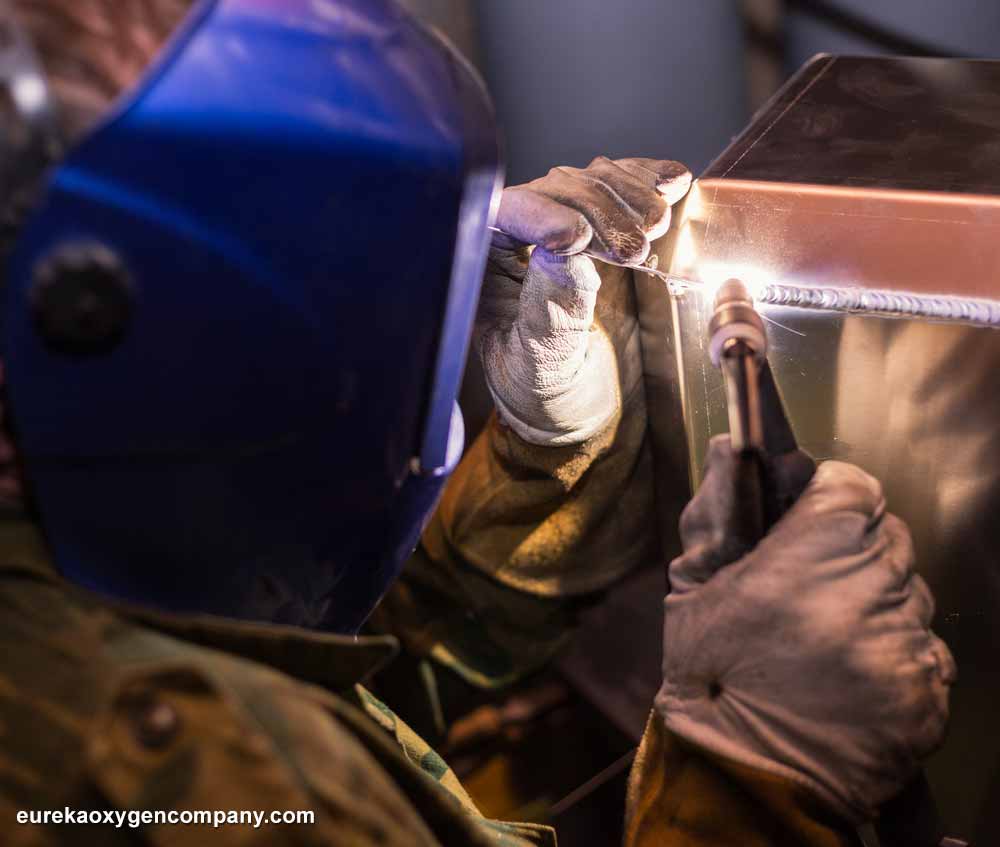
These blends are known to greatly minimize or even completely do away with spatter. In its turn, this minimizes the necessity for intensive post-weld cleanup. Lastly, since they guarantee less wire is wasted thanks to decreased weld spatter, this ensures improved deposition efficiency that, in turn, minimizes the overall cost/hour and labor and wire expenses.
Eureka Oxygen is a leading vendor of a wide variety of industrial gases for welding purposes including argon-oxygen blends. For more details on the welding gas that we stock, and the various welding supplies, welding equipment, and other industrial equipment, please visit our different locations listed here.
Don't Be Shy
Eureka Oxygen is your one-stop-shop for supplies, welding equipment, and expert guidance.
Small task or a big project?
It doesn’t matter; we have what you need.
California Based-Independently Owned