What is the best welding process and equipment for mild steel?
Essentially, the very best welding method for mild steel is MIG welding which is extremely popular with beginners and DIY hobbyists. In this process, a continuous solid wire is fed via the welding gun into the weld pool and ultimately fuses two or more base materials together. At the same time, a shielding gas is relayed through the welding gun, and delivers effective protection against any contamination of the weld pool.
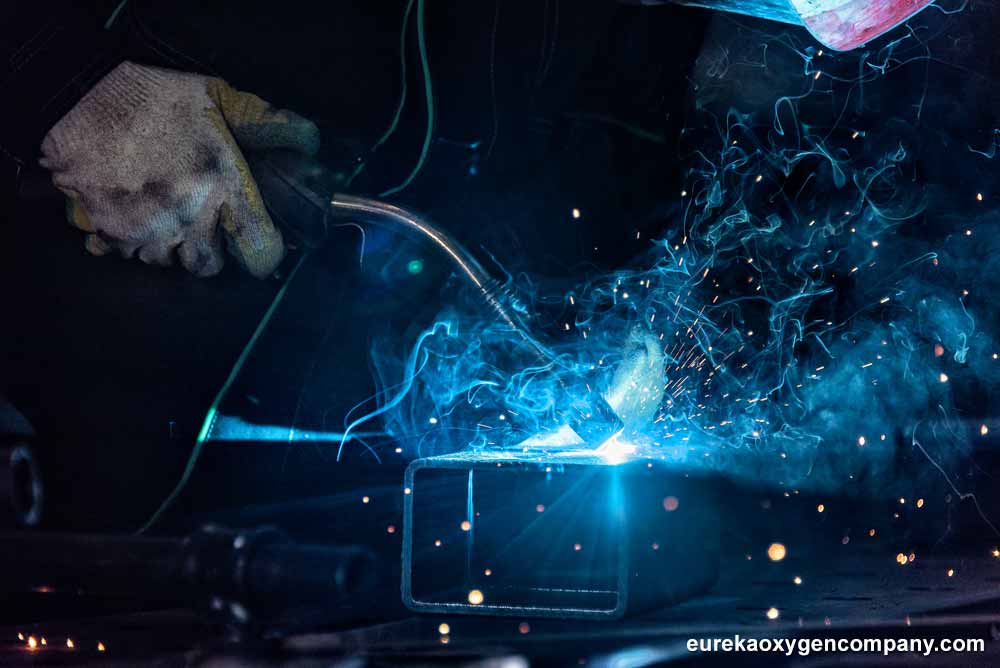
Besides its unparalleled flexibility and versatility, MIG welding is easy to learn and master since the electrode is fed automatically. This permits the welder to focus fully on the welding gun and the material being welded. Let us now look at the main components of equipment used to weld mild steel by the MIG welding process.
Power source (MIG welder)
MIG welders operate on the DC current that delivers a flat and constant voltage. The exact welding current to use at any particular moment can be determined by the speed the wire is fed through the gun, while the arc length can be determined by the voltage level. In MIG welding mild steel, wire burn-off rate can be seamlessly adjusted automatically to compensate for slight variations in 3 key variables. These are the exact distance between the gun and the workpiece, the speed of the wire being fed, and the current pickup rate. MIG welding makes use of 3 different modes of metal transfer, which are pulsed, spray and dip. For thin section metals such as mild steel, a low welding current is utilized.
Wire feed system
To deliver stability and reproducibility, MIG welding relies on the overall performance of the wire feed system. This system needs to be able to feed the wire smoothly, and the welder should always pay close attention to the feed rolls and liners. There are 3 different wire systems utilized in MIG welding, which are pinch rolls, push-pull, and spool-on-gun.
Conduit
The conduit made use in this welding method usually measures a length of no more than 5mm. To facilitate proper wire feeding, this component ought to be kept short and straight at all times.
Welding gun
The welding gun has a number of critical functions. First of all, it directs the wire to the joints. Second, it is the component that transfers the current to the wire, and third, it delivers the shielding gas to protect the weld pool. For welding mild steel, the air-cooled welding gun variety is ideal.
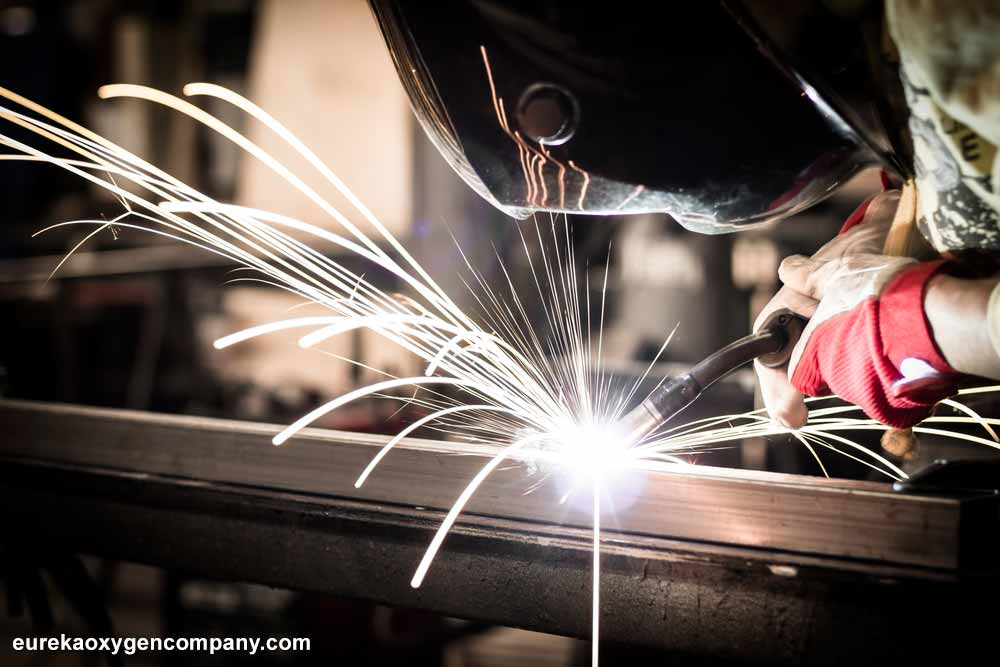
Shielding gas
Generally, there are two main options when it comes to the best shielding gas for MIG welding mild steel. The first is a mixture of 75% argon and 25% CO2 that produces very little spatter, delivers the best bead appearance, and does not encourage burn-through on thin metals like mild steel. Alternatively, some welders use 100% CO2 which delivers a deeper penetration, but inevitably produces much spatter.
Let us now look at the various advancements made in welding carbon steel, particularly in the commercial and manufacturing industries.
Resistance spot welding technology
Resistance spot welding technology is not a new innovation and was first introduced in the early 1900s. However, from its very humble beginnings, this welding technology has evolved into one of the most sophisticated automated welding processes currently in the market. Resistance spot welding is noted for the numerous benefits it delivers over most other welding solutions. This includes its low cost, speed, and strength when it comes to joining sheet metal like mild steel.
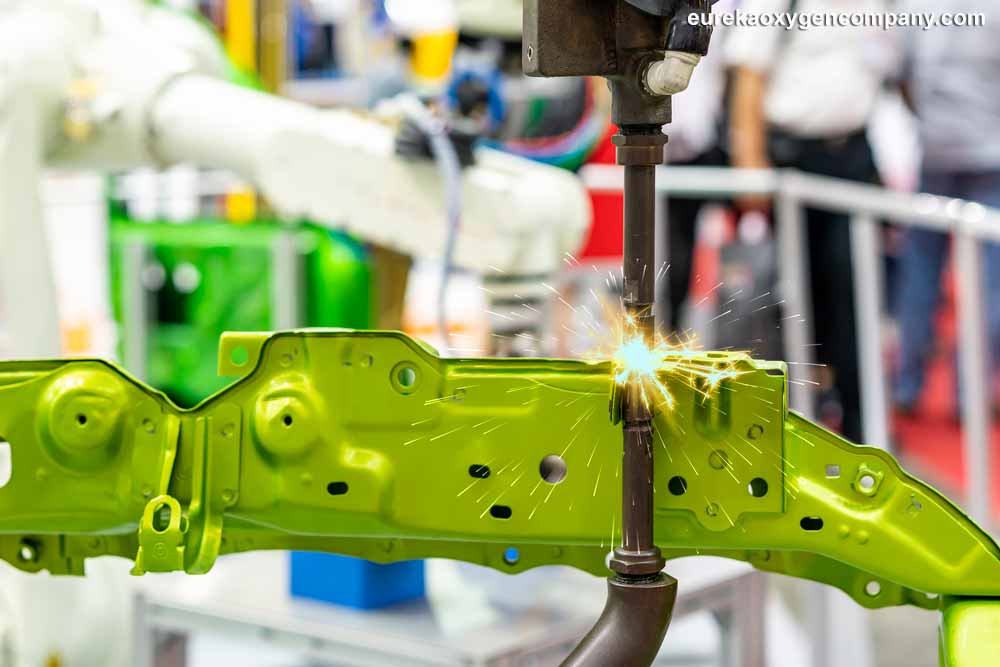
Laser welding technology
Laser welding technology has revolutionized diverse industries in the last 3 decades. It is acclaimed for its unmatched speed, flexibility, suitability for a variety of materials and thicknesses, low distortion, and low heat input. Laser welding also produces deep narrow welds, which makes it practical to create joint configurations that most other welding processes cannot produce.
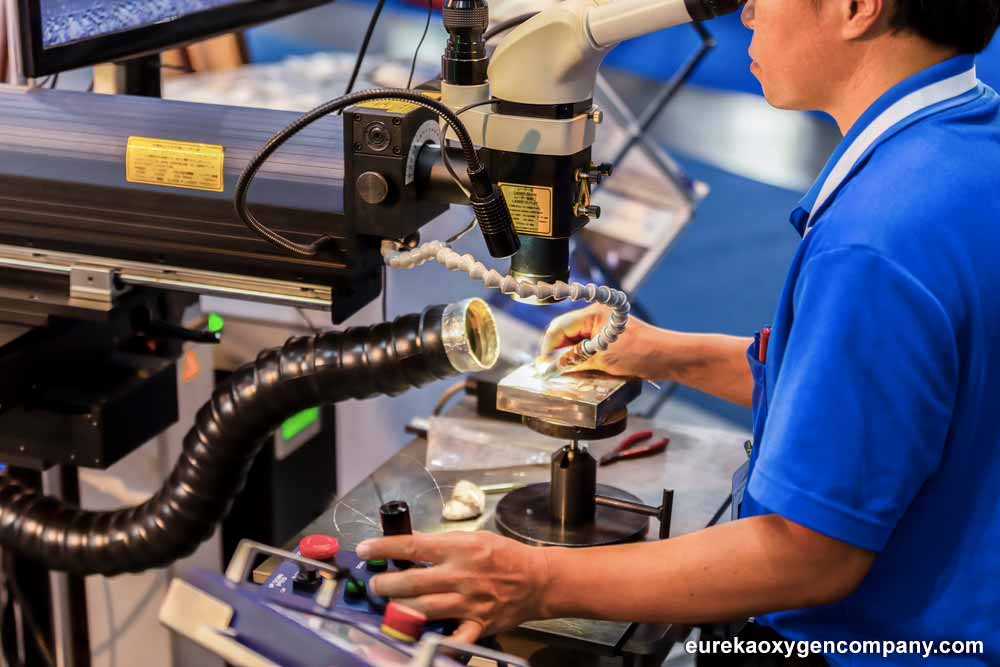
One of the most innovative advances in technology in laser welding would be in the automotive industry. The BrightLine Weld technology permits an extremely flexible range of parameters when it comes to optimizing energy efficiency in welding vehicle components.
Eureka Oxygen is a foremost vendor of a variety of welding equipment, welding supplies and accessories including many designed for welding mild steel that integrate the latest technology and innovations in this industry. We also offer top-quality industrial equipment geared for many industries and trades.